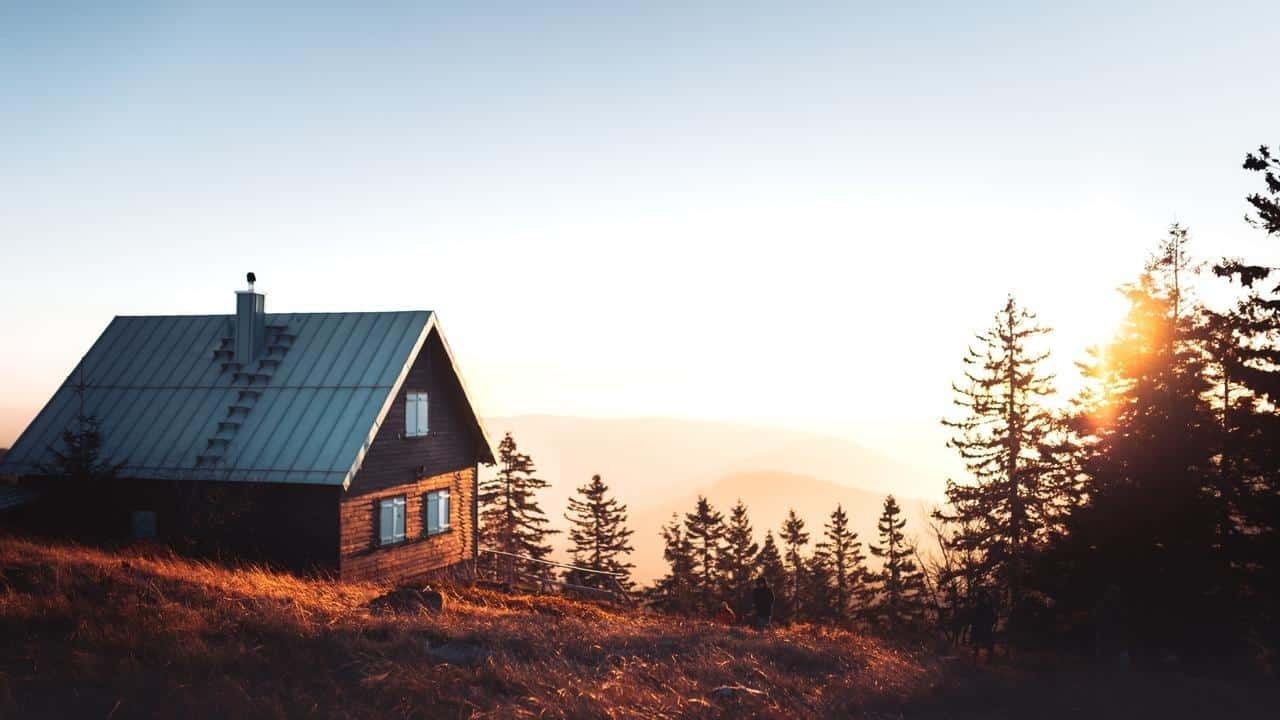
Wood is one of the oldest building materials used by mankind. It was used to build everything from Neolithic longhouses to the first Temple of Jerusalem, built with the cedars of Lebanon. Today, wood frame structures dominate residential construction in the United States. More than 90 percent of American homes are built with wood frames.
However, a number of tragic urban fires—in the United States, the most significant was Chicago’s Great Fire in 1871—led builders to consider other options for taller, higher density buildings. In the late-19th and early-20th centuries, concrete and steel came to dominate the construction of taller buildings. Wood became reserved for interior details, occasionally (when treated) exterior cladding. At most, wood played a supporting role in projects where concrete and steel did the heavy lifting.
That is changing, however, thanks to engineering advances, new protective treatments for lumber, a desire to construct “greener” buildings, and changes to building codes. Wood construction is having another moment beyond the world of residential projects.
Is Wood Construction Safe?
The perception that wood construction presents a greater fire risk isn’t entirely baseless. Dimensional lumber, used in light-frame house construction, does have limited fire resistant capabilities. (We all know that it burns!) Unlike concrete, it needs to be cloaked in protective materials, like gypsum wallboard, for increased fire protection.
But wood does have an advantage over steel when it comes to the threat of fire: the fact that it will burn at the same rate regardless of the temperature of fire. Professional builder and craftsman Jordan Smith explains:
“If steel is exposed to a very hot fire, its strength is going to drop dramatically—nearly to zero—and the building can collapse on itself. With wood, you have the same burn rate. Whether it’s a relatively cold fire or a very hot fire, it is going to burn at the same rate. If a building with a two hour fire rating catches on fire, I know that I’ve got two hours, regardless of what type of fire it is. I have two hours before that’s going to hit the critical size and I’m able to evacuate people safely.”
At the same time, “heavy timber”—larger wood supports—have greater fire resistance as a protective char layer forms when they are exposed to flame.
What is “mass timber”?
“Mass timber” refers to larger projects that are entirely or predominantly built using wooden supports. These buildings include not only heavy timber and dimensional lumber elements, but also new and innovative—and typically fire resistant—products like Cross-Laminated Timber (CLT), Nail-Laminated Timber (NLT), and Glue Laminated Beams (GLB). These materials as well as other design innovations have made mass-timber constructions an increasingly popular—and safe—alternative to concrete and steel designs.
Wood is one of the oldest building materials used by mankind. It was used to build everything from Neolithic longhouses to the first Temple of Jerusalem, built with the cedars of Lebanon. Today, wood frame structures dominate residential construction in the United States. More than 90 percent of American homes are built with wood frames.
However, a number of tragic urban fires—in the United States, the most significant was Chicago’s Great Fire in 1871—led builders to consider other options for taller, higher density buildings. In the late-19th and early-20th centuries, concrete and steel came to dominate the construction of taller buildings. Wood became reserved for interior details, occasionally (when treated) exterior cladding. At most, wood played a supporting role in projects where concrete and steel did the heavy lifting.
That is changing, however, thanks to engineering advances, new protective treatments for lumber, a desire to construct “greener” buildings, and changes to building codes. Wood construction is having another moment beyond the world of residential projects.
Is Wood Construction Safe?
The perception that wood construction presents a greater fire risk isn’t entirely baseless. Dimensional lumber, used in light-frame house construction, does have limited fire resistant capabilities. (We all know that it burns!) Unlike concrete, it needs to be cloaked in protective materials, like gypsum wallboard, for increased fire protection.
But wood does have an advantage over steel when it comes to the threat of fire: the fact that it will burn at the same rate regardless of the temperature of fire. Professional builder and craftsman Jordan Smith explains:
“If steel is exposed to a very hot fire, its strength is going to drop dramatically—nearly to zero—and the building can collapse on itself. With wood, you have the same burn rate. Whether it’s a relatively cold fire or a very hot fire, it is going to burn at the same rate. If a building with a two hour fire rating catches on fire, I know that I’ve got two hours, regardless of what type of fire it is. I have two hours before that’s going to hit the critical size and I’m able to evacuate people safely.”
At the same time, “heavy timber”—larger wood supports—have greater fire resistance as a protective char layer forms when they are exposed to flame.
What is “mass timber”?
“Mass timber” refers to larger projects that are entirely or predominantly built using wooden supports. These buildings include not only heavy timber and dimensional lumber elements, but also new and innovative—and typically fire resistant—products like Cross-Laminated Timber (CLT), Nail-Laminated Timber (NLT), and Glue Laminated Beams (GLB). These materials as well as other design innovations have made mass-timber constructions an increasingly popular—and safe—alternative to concrete and steel designs.
In 2019, the International Code Council adopted 14 measures related to mass-timber constructions that will be incorporated into the 2021 edition of the International Building Code. While previously the code allowed for mass-timber buildings up to six stories, the new code extends that limit up to 18 stories. This will surely help fuel the revived interest in wood construction.
Learn all about the properties of wood and how wood is used in construction in the MT Copeland course on Wood Materials. Taught by professional builder Jordan Smith, the course covers topics that range from I-joists to shear strength.
What are the advantages and disadvantages of light wood construction?
In the United States, the vast majority of homes are built with wood frames: the material is plentiful and familiar—builders know how to quickly construct a wood frame house. On the other hand, almost all taller buildings in the United States, whether apartment blocks or office towers, have long been built using steel and concrete, in part thanks to safety concerns and building codes. Sometimes, however, the old rules don’t always apply.
Advantages of wood construction
- Simplicity of construction. The wood beams, joists, and studs can be cut to size onsite and, unlike some other construction materials, no heavy equipment is required.
- Speed of construction. While the frame is generally built on site, some elements can be prefabricated allowing for greater control of details and less time in construction.
- Sustainability. Wooden buildings are, unlike concrete and steel ones, made from a renewable resource and one that is especially abundant in North America: trees.
- Carbon-capture benefits. Over the course of its life cycle, trees remove carbon from the air, but they return that captured carbon into the soil and the atmosphere when they eventually decompose. When wood is used in the construction of a house, however, the carbon remains trapped, at least as long as the building still stands.
- Insulation. Compared to other materials like glass, concrete, and steel, wood has low-thermal conductivity—in other words, it retains heat and makes for a more energy efficient home.
- Improved air quality. Some studies indicate that the air quality in wood buildings is better, with fewer toxic emissions compared to some other construction materials.
Disadvantages
- Wood rot. While huge advances have been made in the treatment of wood to extend its life span, it still remains more subject to rot than concrete. Mold and mildew can also be concerns with wood construction, though they can also be avoided if attention is paid to moisture control, properly sealing windows, and taking other preventative measures.
- Structural limitations. Wood is an excellent choice for many traditional houses, especially those in a timber frame style. Some design features found in more contemporary houses, however, like cantilevered elements or large windows, can be difficult to achieve relying on wood frame construction. Concrete and steel structures may be more appropriate choices for some contemporary home designs.
- Fire risks. The application of fire retardants and the installation of sprinkler systems can limit the risk of fire in completed wood-frame buildings, but builders should be aware of the fire hazards in the early stages of construction, when the wood frame is largely exposed and unprotected.
- Building code limitations. While the International Code Council has become more accepting of wood construction, in general these buildings still cannot be as tall as others. Recent changes to building codes have, however, created more alternatives. For example, a 2015 update allows for construction of wood structures atop concrete podiums, allowing mostly wood constructions to reach new heights.
Many of the disadvantages of wood as a construction material are diminishing thanks to advances by chemists, engineers, and others. Builder Jordan Smith sees reasons for optimism about wood constructions’ future: “We’ve been building with this for 6,000—maybe 10,000 years,” Smith says.
“Advances that we’ve been making on the engineering side will really push wood into the future of framing.”
MT Copeland offers video-based online classes that give you a foundation in construction fundamentals with real-world applications. Classes include professionally produced videos taught by practicing craftspeople, and supplementary downloads like quizzes, blueprints, and other materials to help you master the skills.