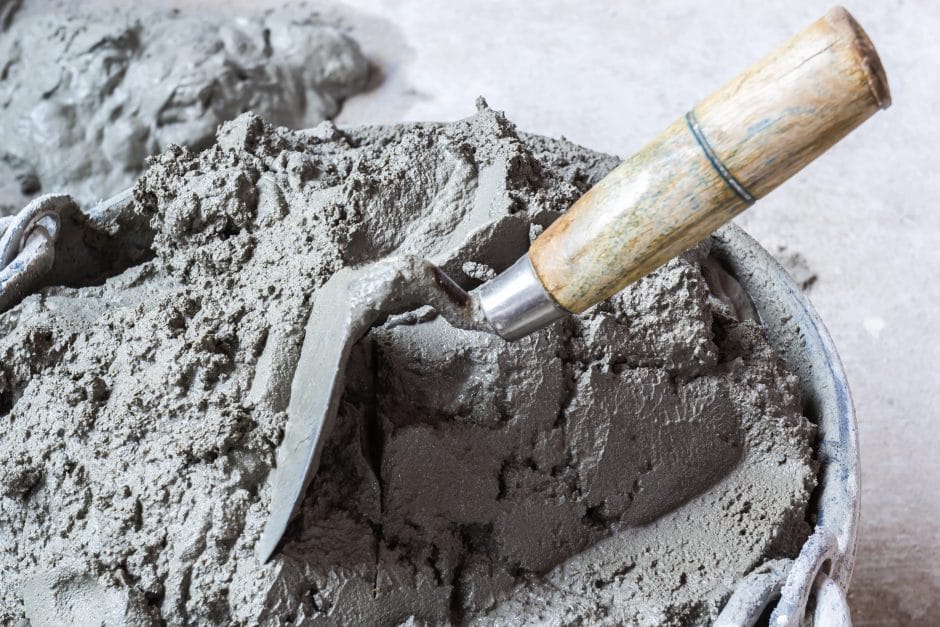
After good old-fashioned water, concrete is the second-most used material in the world. There are many different types of concrete but they all follow the same basic mixing and production method. Learn what goes into concrete and how concrete is made.
What is concrete?
Concrete is a hardened mixture of paste and rocks, also known as aggregates, that is used as a building material for durable structures like buildings and bridges. When fresh concrete is initially mixed, it is pliable and plastic-like. Hardened concrete, on the other hand, is sturdy and extremely tough.
What is concrete made of?
Concrete is made of aggregates, Portland cement, and water. The three raw materials used to make concrete each play a different chemical role in the formation of concrete.
- Portland cement. The Portland cement is made of calcareous material containing calcium compounds (often made from limestone, clay, fly ash, sandstone, or shale), alumina, silica, and iron oxide. The ingredients are crushed up, heated in a kiln, and ground up again to create the Portland cement. When combined with water, a chemical reaction that occurs is that it forms a paste, which coats and eventually binds the aggregate.
- Water. Portland cement is what is referred to as a “hydraulic cement,” which means it gets its strength from its chemical reaction with water. The aluminate reacts with the H2O in a chemical reaction called hydration. Through this process, the paste becomes stronger and hardens into a tougher material.
- Aggregates. The aggregates are typically composed of both fine sand and coarse rock, like crushed stone or gravel. The aggregates make up about 75% of the concrete are the main reason it is so structurally durable. Different types of rock used for aggregates include granite, basalt, flint, and pozzolana, which comes from volcanic ash and makes the concrete denser.
- Admixtures. Various chemicals, called admixtures, can also be added to concrete to make different sorts of mixtures. Different admixtures have different purposes, such as accelerating the setting time of the concrete, making the concrete generally easier to work with and finish, or making the concrete stronger by lowering the water to cement ratio.
What are the common types of concrete?
Different types of concrete are made based on their mixing proportions. Some common concrete mixes include:
- Normal strength concrete. This concrete mixture is made of cement, aggregates, and water and has a mixing proportion of 1:2:4 (one part cement, two parts aggregate, four parts water). The amount of water used will depend on the humidity of the location and the desired consistency of the concrete. Normal concrete is typically used for pavements, home construction projects, and buildings that don’t require maximum tensile strength.
- High-strength concrete. High-strength concrete is a type of concrete with a compressive strength of over 6000 PSI. Compared to normal strength concrete, high-strength concrete carries heavy loads more efficiently while also being more lightweight (because less material is used). This type of concrete is typically used to build high-rise buildings.
- Prestressed concrete. Prestressed concrete is concrete that has compressive stresses applied to it during production. These initial compressive stresses, induced by steel tendons, are engineered to counteract the stresses that will eventually be placed upon the concrete during service. It combines the high tensile strength of steel and the high compressive characteristic of concrete. Since the concrete is formed under stress, a prestressed concrete structure will be more balanced and less likely to crack when holding heavy loads. Bridges, roofs, and flooring are often made using prestressed concrete.
- Pervious concrete. Pervious concrete is composed of water, cement, and coarse aggregates. Fine aggregates, like sand, are not used in pervious concrete, which causes it to be more porous and allows water to pass through it quickly and with more ease. This type of concrete is used to build roads and pavements and places that deal with stormwater buildup. Some pervious concrete can absorb water at a rate of up to five gallons a minute, where it is absorbed into the earth below.
- High-density concrete. High-density concrete is made using heavyweight aggregates that aid in resistance to radiation, which is why this type of concrete is often used to construct atomic power plants. Compared to other types of concrete, high-density concrete is usually around 50% denser, with a density level of 3360 kg/m3 to 3840 kg/m3. In the event that an even denser concrete is necessary, using iron as both the fine aggregate and the coarse aggregate can increase the level of density to 5200kg/m3.
- Lightweight concrete. Lightweight concrete is known for having low thermal conductivity and is made using lightweight aggregates, such as pumice, clay, or perlite. Since the specific aggregates chosen are what determines the density of the concrete, lightweight concrete is low in density, and is defined as any type of concrete with a density level of less than 1920kg/m3.
How is concrete made?
Concrete is made by combining the Portland cement with water to create a paste that coats the aggregates and bonds together and gains strength as it hardens. The process involves several steps:
After good old-fashioned water, concrete is the second-most used material in the world. There are many different types of concrete but they all follow the same basic mixing and production method. Learn what goes into concrete and how concrete is made.
What is concrete?
Concrete is a hardened mixture of paste and rocks, also known as aggregates, that is used as a building material for durable structures like buildings and bridges. When fresh concrete is initially mixed, it is pliable and plastic-like. Hardened concrete, on the other hand, is sturdy and extremely tough.
What is concrete made of?
Concrete is made of aggregates, Portland cement, and water. The three raw materials used to make concrete each play a different chemical role in the formation of concrete.
- Portland cement. The Portland cement is made of calcareous material containing calcium compounds (often made from limestone, clay, fly ash, sandstone, or shale), alumina, silica, and iron oxide. The ingredients are crushed up, heated in a kiln, and ground up again to create the Portland cement. When combined with water, a chemical reaction that occurs is that it forms a paste, which coats and eventually binds the aggregate.
- Water. Portland cement is what is referred to as a “hydraulic cement,” which means it gets its strength from its chemical reaction with water. The aluminate reacts with the H2O in a chemical reaction called hydration. Through this process, the paste becomes stronger and hardens into a tougher material.
- Aggregates. The aggregates are typically composed of both fine sand and coarse rock, like crushed stone or gravel. The aggregates make up about 75% of the concrete are the main reason it is so structurally durable. Different types of rock used for aggregates include granite, basalt, flint, and pozzolana, which comes from volcanic ash and makes the concrete denser.
- Admixtures. Various chemicals, called admixtures, can also be added to concrete to make different sorts of mixtures. Different admixtures have different purposes, such as accelerating the setting time of the concrete, making the concrete generally easier to work with and finish, or making the concrete stronger by lowering the water to cement ratio.
What are the common types of concrete?
Different types of concrete are made based on their mixing proportions. Some common concrete mixes include:
- Normal strength concrete. This concrete mixture is made of cement, aggregates, and water and has a mixing proportion of 1:2:4 (one part cement, two parts aggregate, four parts water). The amount of water used will depend on the humidity of the location and the desired consistency of the concrete. Normal concrete is typically used for pavements, home construction projects, and buildings that don’t require maximum tensile strength.
- High-strength concrete. High-strength concrete is a type of concrete with a compressive strength of over 6000 PSI. Compared to normal strength concrete, high-strength concrete carries heavy loads more efficiently while also being more lightweight (because less material is used). This type of concrete is typically used to build high-rise buildings.
- Prestressed concrete. Prestressed concrete is concrete that has compressive stresses applied to it during production. These initial compressive stresses, induced by steel tendons, are engineered to counteract the stresses that will eventually be placed upon the concrete during service. It combines the high tensile strength of steel and the high compressive characteristic of concrete. Since the concrete is formed under stress, a prestressed concrete structure will be more balanced and less likely to crack when holding heavy loads. Bridges, roofs, and flooring are often made using prestressed concrete.
- Pervious concrete. Pervious concrete is composed of water, cement, and coarse aggregates. Fine aggregates, like sand, are not used in pervious concrete, which causes it to be more porous and allows water to pass through it quickly and with more ease. This type of concrete is used to build roads and pavements and places that deal with stormwater buildup. Some pervious concrete can absorb water at a rate of up to five gallons a minute, where it is absorbed into the earth below.
- High-density concrete. High-density concrete is made using heavyweight aggregates that aid in resistance to radiation, which is why this type of concrete is often used to construct atomic power plants. Compared to other types of concrete, high-density concrete is usually around 50% denser, with a density level of 3360 kg/m3 to 3840 kg/m3. In the event that an even denser concrete is necessary, using iron as both the fine aggregate and the coarse aggregate can increase the level of density to 5200kg/m3.
- Lightweight concrete. Lightweight concrete is known for having low thermal conductivity and is made using lightweight aggregates, such as pumice, clay, or perlite. Since the specific aggregates chosen are what determines the density of the concrete, lightweight concrete is low in density, and is defined as any type of concrete with a density level of less than 1920kg/m3.
How is concrete made?
Concrete is made by combining the Portland cement with water to create a paste that coats the aggregates and bonds together and gains strength as it hardens. The process involves several steps:
- Make the Portland cement. The first step to making concrete is preparing the Portland cement mix. Calcareous material is ground up into a fine powder, heated, then burned in a rotary. This turns it into a material called clinker, which is ground up again until it is a fine, crushed powder.
- Proportioning process. Before concrete is made, the ingredients that make it up must be proportioned correctly to ensure the outcome of a mixture that is strong and sturdy. The components of concrete react differently with each other based on the ratio of how much of each is added.
- Mixing. This is followed by mixing the cement with the aggregates, water, and, if necessary, admixtures. The ingredients are stirred together well, as to properly coat the aggregates with the cement paste.
- Hydrating. After the ingredients are proportioned and mixed together, a chemical reaction known as hydration immediately begins. This is when the cement is activated by the water and starts to gain strength, coating the aggregate particles.
- Placement. Once the concrete has undergone hydration, it needs to be placed before becoming too hardened. Placing concrete is accomplished using hoppers, chutes, buckets. Concrete placement can vary based on the type of concrete mixture, what is actually being built, the location, and the weather of the location.
- Curing. Once the top level of the concrete has hardened, curing can begin. In order for the concrete to gain adequate strength, it must be continuously kept well hydrated and moist. Curing techniques can include covering the concrete with moistened fabrics, spraying it with a curing compound spray, or covering it in water fog. Curing is also dependent on the type of concrete and the weather of the location.
MT Copeland offers video-based online classes that give you a foundation in construction fundamentals with real-world applications, like plumbing basics. Classes include professionally produced videos taught by practicing craftspeople, and supplementary downloads like quizzes, blueprints, and other materials to help you master the skills.