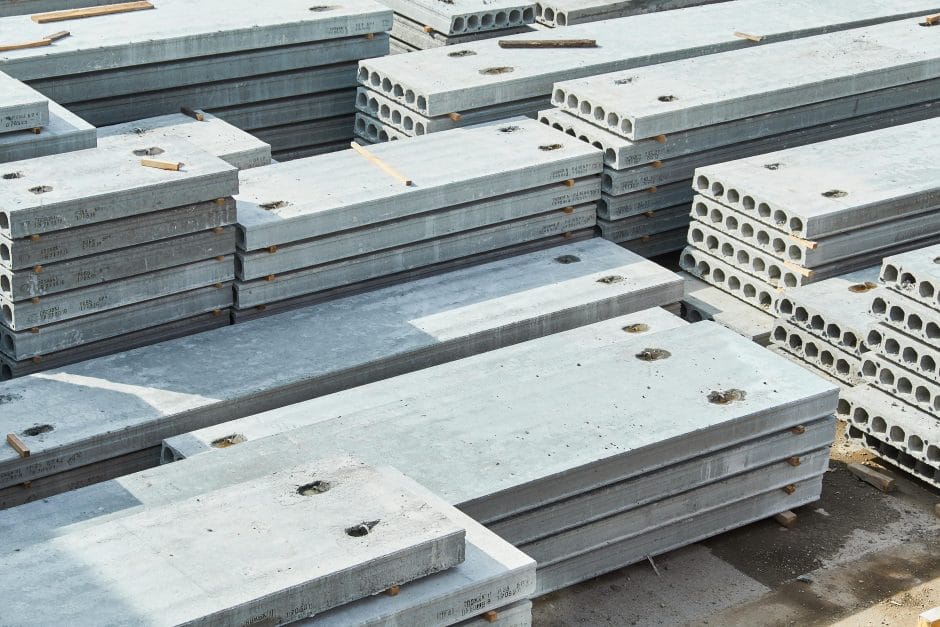
Concrete is the most used building material in the world not only because of its strength but also because of its ability to be molded in many different shapes. Oftentimes, a structure requires many pieces of concrete in the same shape and size. This is the benefit of precast concrete, where manufacturers are able to make molds to specific sizes to form multiple pieces of concrete, speeding up the overall construction process.
What is precast concrete?
Precast concrete refers to the concrete part or piece of a structure that is made in one place and transferred to another for use. The concrete is cast in a mold, cured in a controlled environment, and then transferred to the construction site where it will actually be put in place. Oftentimes this mold is reusable, which is why precast concrete is frequently used for making uniform pieces of a structure, like the multiple rectangular pieces of concrete used to create the wall panels of a concrete framed building.
Precast concrete is often stronger since the concrete is cured in a location specifically controlled to accommodate the best possible conditions for the concrete to set. This, paired with the fact that precast concrete is often reinforced with steel rebar, is a recipe for increased strength and long-term ability to withstand heavy loads and traffic.
What are the types of precast concrete?
Common types of precast products include the following:
- Bridge beams. Precast concrete is used to make many aspects of bridge systems, including beams, deck slabs, archers, and girders.
- Double Ts. This refers to a precast concrete structural product used for buildings that need support heavy loads, such as a parking structure, roof, or bridge. A double T (or double tee) is a flat slab of concrete with two beams underneath, resembling two I-beams attached together.
- Hollow-core slabs. A hollow-core slab, a plank of concrete with hollowed-out tunnels inside of it, extending the full length of the concrete slab, is a precast concrete plank used in multi-story housing buildings, such as big apartment buildings. The hollow cores This allows the slab to be lighter in weight reduce the overall weight of the structure.
- Septic tanks/manholes. Quality precast concrete is commonly used in the construction of septic tanks needing to withstand heavy water and soil loads. Since manufacturing precast concrete is done in a controlled environment with efficient quality control methods which enables the concrete to be strong, durable, and corrosion-resistant. Precast concrete is also the preferred material used to make manholes, which need to be a uniform size and style enabling the use of reusable molds.
- Pipes/culverts. The most widely used type of concrete piping is precast piping. Precast concrete box culverts are versatile and are used for many architectural endeavors, such as tunnels, bridges, subways, road crossings, underpasses, and storage. Precast concrete is ideal for these structures because the pieces are a uniform shape and style, meaning builders can use reusable precast concrete molds.
- Foundational walls. High-strength, lightweight precast concrete is often used to build foundations and basements. Although they are thinner and lighter, they provide more strength than a concrete blocks, and are more resistant than other types of walls to fire, termites, and dry rot.
- Steps. Precast concrete steps are widely used for entrances to residential and commercial buildings. A precast concrete step is easy to install, durable, and generally very low maintenance. Steps are an ideal candidate for a precast concrete method since they are usually smaller in size and therefore are easily transferable from a mixing site to the installation site. Since steps are usually uniform, the precast molds mean that many steps can be made at a time using the same mold shape.
- Traffic barriers/retaining walls. Precast concrete retaining walls are often used as protective traffic barriers on structures, like freeways and roads, that have a lot of pedestrian and vehicular traffic on them. The precast method is ideal for these types of concrete structures because of the quick installation process, keeping traffic disruptions to a minimum. A traffic structure built using precast concrete can be placed upon arrival, has high durability and strength due to extra quality control measures an offsite plant offers, and the precast molds and forms help keep structures and pieces uniform.
What are the advantages of using precast concrete?
Projects that call for multiple uniform concrete pieces can take advantage of the precast method for making them. Precast concrete has a few distinct advantages.
- Uniform size and shape. Precast concrete has the ability for pieces to be uniform in size. The molds manufacterers use to cast concrete are specifically configured for the job. This means concrere pieces are guaranteed to be the size and shape necessary for a proejct, with exacting dimension.
- Speed of construction. These molds can be reused several times and enable builders to make a lot of uniform concrete pieces in a short amount of time, resulting in faster construction times overall.
- Time efficiency. Since it’s made offsite, precast concrete is ready to be installed without any waiting time for it to gain strength, thereby speeding up the overall construction process. Plus, accelerated curing processes made possible with technology engineered at a plant or factory mean that the precast concrete gets to a higher strength, quicker.
- Quality control. Precast concrete is constructed at a site or plant that is specifically meant to do so. Therefore, casting concrete in this environment will be more controlled and surveilled, opposed to concrete being made at a construction site with complete technical control.
What are the downsides of using precast concrete?
While many project owners and builders may find the advantages of using precast concrete work in their favor, there are a few disadvantages to keep in mind.
Concrete is the most used building material in the world not only because of its strength but also because of its ability to be molded in many different shapes. Oftentimes, a structure requires many pieces of concrete in the same shape and size. This is the benefit of precast concrete, where manufacturers are able to make molds to specific sizes to form multiple pieces of concrete, speeding up the overall construction process.
What is precast concrete?
Precast concrete refers to the concrete part or piece of a structure that is made in one place and transferred to another for use. The concrete is cast in a mold, cured in a controlled environment, and then transferred to the construction site where it will actually be put in place. Oftentimes this mold is reusable, which is why precast concrete is frequently used for making uniform pieces of a structure, like the multiple rectangular pieces of concrete used to create the wall panels of a concrete framed building.
Precast concrete is often stronger since the concrete is cured in a location specifically controlled to accommodate the best possible conditions for the concrete to set. This, paired with the fact that precast concrete is often reinforced with steel rebar, is a recipe for increased strength and long-term ability to withstand heavy loads and traffic.
What are the types of precast concrete?
Common types of precast products include the following:
- Bridge beams. Precast concrete is used to make many aspects of bridge systems, including beams, deck slabs, archers, and girders.
- Double Ts. This refers to a precast concrete structural product used for buildings that need support heavy loads, such as a parking structure, roof, or bridge. A double T (or double tee) is a flat slab of concrete with two beams underneath, resembling two I-beams attached together.
- Hollow-core slabs. A hollow-core slab, a plank of concrete with hollowed-out tunnels inside of it, extending the full length of the concrete slab, is a precast concrete plank used in multi-story housing buildings, such as big apartment buildings. The hollow cores This allows the slab to be lighter in weight reduce the overall weight of the structure.
- Septic tanks/manholes. Quality precast concrete is commonly used in the construction of septic tanks needing to withstand heavy water and soil loads. Since manufacturing precast concrete is done in a controlled environment with efficient quality control methods which enables the concrete to be strong, durable, and corrosion-resistant. Precast concrete is also the preferred material used to make manholes, which need to be a uniform size and style enabling the use of reusable molds.
- Pipes/culverts. The most widely used type of concrete piping is precast piping. Precast concrete box culverts are versatile and are used for many architectural endeavors, such as tunnels, bridges, subways, road crossings, underpasses, and storage. Precast concrete is ideal for these structures because the pieces are a uniform shape and style, meaning builders can use reusable precast concrete molds.
- Foundational walls. High-strength, lightweight precast concrete is often used to build foundations and basements. Although they are thinner and lighter, they provide more strength than a concrete blocks, and are more resistant than other types of walls to fire, termites, and dry rot.
- Steps. Precast concrete steps are widely used for entrances to residential and commercial buildings. A precast concrete step is easy to install, durable, and generally very low maintenance. Steps are an ideal candidate for a precast concrete method since they are usually smaller in size and therefore are easily transferable from a mixing site to the installation site. Since steps are usually uniform, the precast molds mean that many steps can be made at a time using the same mold shape.
- Traffic barriers/retaining walls. Precast concrete retaining walls are often used as protective traffic barriers on structures, like freeways and roads, that have a lot of pedestrian and vehicular traffic on them. The precast method is ideal for these types of concrete structures because of the quick installation process, keeping traffic disruptions to a minimum. A traffic structure built using precast concrete can be placed upon arrival, has high durability and strength due to extra quality control measures an offsite plant offers, and the precast molds and forms help keep structures and pieces uniform.
What are the advantages of using precast concrete?
Projects that call for multiple uniform concrete pieces can take advantage of the precast method for making them. Precast concrete has a few distinct advantages.
- Uniform size and shape. Precast concrete has the ability for pieces to be uniform in size. The molds manufacterers use to cast concrete are specifically configured for the job. This means concrere pieces are guaranteed to be the size and shape necessary for a proejct, with exacting dimension.
- Speed of construction. These molds can be reused several times and enable builders to make a lot of uniform concrete pieces in a short amount of time, resulting in faster construction times overall.
- Time efficiency. Since it’s made offsite, precast concrete is ready to be installed without any waiting time for it to gain strength, thereby speeding up the overall construction process. Plus, accelerated curing processes made possible with technology engineered at a plant or factory mean that the precast concrete gets to a higher strength, quicker.
- Quality control. Precast concrete is constructed at a site or plant that is specifically meant to do so. Therefore, casting concrete in this environment will be more controlled and surveilled, opposed to concrete being made at a construction site with complete technical control.
What are the downsides of using precast concrete?
While many project owners and builders may find the advantages of using precast concrete work in their favor, there are a few disadvantages to keep in mind.
- Must be transported correctly. Since it’s manufactured offsite, and sometimes far away, reliable transportation will be necessary when using precast concrete. A trailer must be used to do this, which can be costly. Precast concrete also must be handled correctly during transportation to prevent damage.
- Difficult to modify. Once the precast concrete is made, it’s hard to modify. Doing so can result in safety issues and the concrete will no longer be stable. If the measurements are wrong, however, you’ll need to order completely new pieces, which will mean higher costs and delays.
- Requires careful installation. In a standard poured concrete application, workers only have to pour the concrete, but with precast, you’ll need workers properly trained to move heavy concrete around carefully, as well as connect the pieces together correctly. In some instances, a crane may be needed to place pieces where they need to go, which will be an additional cost.
MT Copeland offers video-based online classes that give you a foundation in construction fundamentals with real-world applications, like plumbing basics. Classes include professionally produced videos taught by practicing craftspeople, and supplementary downloads like quizzes, blueprints, and other materials to help you master the skills.