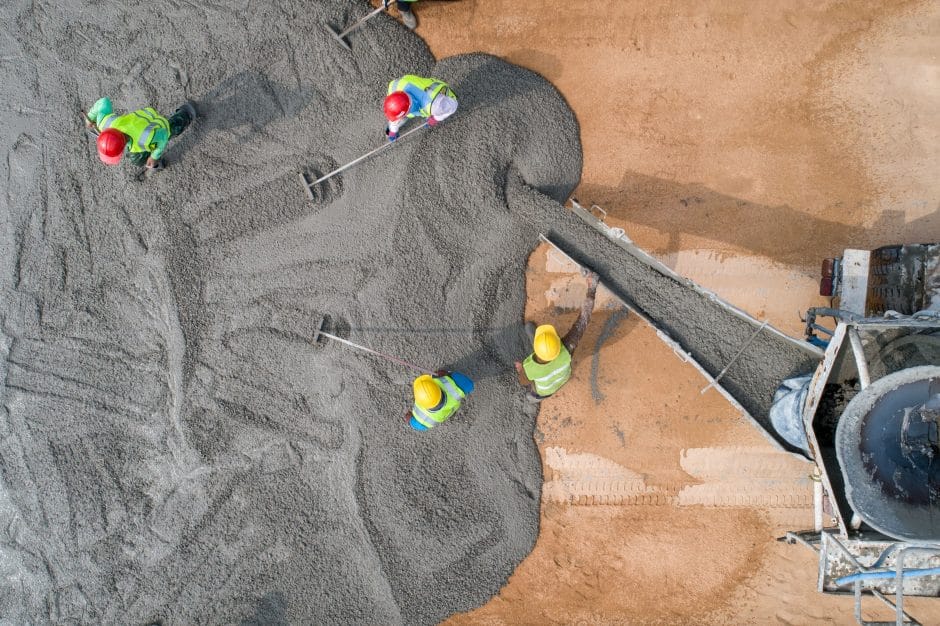
Concrete is the most popular construction material in the world. In fact, it’s the second most used material in the world (water reigns supreme at number one). Almost every kind of construction involves concrete in some way, and it’s used to build everything from highways to bridges and skyscrapers to parking structures. Concrete is resilient in that it does not rust, rot, or burn. The use of concrete as a building material is essential to buildings due to its durability, strength, and extreme longevity.
What are the basic properties of concrete?
The basic properties of concrete are fine and coarse aggregates (like sand and rocks or pebbles), Portland cement, and water. These three raw materials each play a different chemical role in the formation of concrete, as Portland cement is a hydraulic cement meaning it gets its strength from its chemical reaction with water. When Portland cement and water combine, a chemical reaction called hydration occurs. Through this process, the paste coats the aggregates and bonds them together, gaining strength as it hardens, and concrete is created.
When making concrete, builders use fine aggregate to add volume, while coarse aggregate provides the strength necessary to carry heavy loads. Various chemicals, called admixtures, can also be added to concrete to make different sorts of mixtures.
How is concrete made?
Before concrete is made, the three raw materials must be proportioned correctly to ensure the outcome of a mixture that is strong and sturdy. The components of concrete react differently with each other based on the ratio of how much of each is added, and proportions will differ based on the type of concrete being made. The most common ratio, however, is:
- 10–15% cement
- 60–75% aggregate
- 15–20% water
The concrete mixing process begins with preparing the Portland cement mix. Portland cement is made of a calcareous material (often limestone) that is ground up into a powder, which is then heated and burned in a rotary, turning it into a pebble-like material called “clinker” The clinker is then ground up again until it is a crushed powder, to which gypsum is added.
After the Portland cement is prepared, it is mixed with the aggregates, water, and optional admixtures (the different chemicals or materials that change the consistency and strength of concrete). The ingredients are stirred together well, as to properly coat the aggregates with the cement paste. After combining the materials, the cement is activated by the water, coating the aggregate particles and gaining strength as it hardens in a process called hydration.
16 Common types of concrete
One of the reasons concrete is used to build so many different structures is due to how versatile it is and how it can be molded to any desired shape or design. There are many different types of concrete, however, and they are used for all different sorts of structures. Here are 16 types of concrete and how they are used.
1. Normal strength concrete
Normal strength concrete, or “regular” concrete, is the most common type of concrete with a basic mix of cement, aggregates, and water. Normal concrete has a mixing proportion of 1:2:4 (one part cement, two parts aggregate, four parts water), however, the amount of water used will depend on the humidity of the location and the desired consistency of the concrete. Normal strength concrete is typically used for pavements, home construction projects, and buildings that don’t require maximum tensile strength.
2. Plain concrete
Plain concrete is concrete in its simplest form. It is made using the same mixing proportions as normal strength concrete, but will have absolutely no reinforcement in it. It can be used to build structures that do not require intense tensile strength. Pavements and walkways are common uses of plain concrete.
3. Lightweight concrete
This type of concrete has a lower density and a higher water content than normal concrete. Lightweight concrete is made using lightweight aggregates, such as pumice, clay, or perlite. Since the specific aggregates chosen are what determines the density of the concrete, lightweight concrete is low in density, and is defined as any type of concrete with a density level of less than 1920kg/m3. Lightweight concrete is used in areas where the total “dead weight” of a building can be reduced to help prevent collapse, such as walls or flooring.
4. Ready mix concrete
Ready mix concrete is made at a manufacturing plant and delivered to a construction site using a truck with a mixer attached to it. It usually contains admixtures to make it so the cement doesn’t harden before arriving at the site, and is ready to pour.
5. Polymer concrete
Polymer concrete is concrete in which the lime and shale-based Portland cement is replaced with a polymer binder that cures and hardens, such as a polyester, epoxy mixtures, vinyl ester, acrylics, or many various types of polymer resins. The objective of polymer concrete depends on the type of resin used. Epoxy binders, for example, will aid in less shrinkage during curing while acrylic binders offer weather resistance and quicker setting times. Polymer plastic is stickier than cement, and therefore, when combined in a concrete mix, leads to a concrete of higher tensile strength than one composed of Portland cement. When mixing together a polymer binder with water and aggregates, a chemical reaction occurs that begins the curing process quicker than regular concrete. Polymer concrete has a good resistance to corrosion which is why it is used in swimming pools, sewer structures, and other structures that come into close contact with liquids and corrosion-causing chemicals.
6. Glass concrete
Concrete is referred to as glass concrete when recycled glass is added as an aggregate, or used in places of both fine and coarse aggregates, depending on the desired outcome. Glass aggregates are almost always made from recycled glass and can range in size from a fine talc-like powder to gravel-side pieces to six-inch glass rocks. Glass can be crushed using a glass crushing machine, or used in chunks when mixed with the cement, depending on the desired look. Glass concrete typically has a shiny or “glowing” look to it, which makes it an aesthetically pleasing and highly polished looking option for countertops, floors, and tiles.
7. Reinforced concrete
Reinforced concrete, also known as reinforced cement concrete, is made with reinforced bars, usually rebar, to improve the tensile strength of the concrete. The compressive strength of the concrete paired with the tensile strength of the reinforcement material improves the concrete’s overall durability. Contractors might encounter reinforced concrete in large-scale structures that require an immense amount of tensile strength, such as tall buildings, bridges, dams, or any construction situation that involves a structure needing to carry extremely heavy loads.
Concrete is the most popular construction material in the world. In fact, it’s the second most used material in the world (water reigns supreme at number one). Almost every kind of construction involves concrete in some way, and it’s used to build everything from highways to bridges and skyscrapers to parking structures. Concrete is resilient in that it does not rust, rot, or burn. The use of concrete as a building material is essential to buildings due to its durability, strength, and extreme longevity.
What are the basic properties of concrete?
The basic properties of concrete are fine and coarse aggregates (like sand and rocks or pebbles), Portland cement, and water. These three raw materials each play a different chemical role in the formation of concrete, as Portland cement is a hydraulic cement meaning it gets its strength from its chemical reaction with water. When Portland cement and water combine, a chemical reaction called hydration occurs. Through this process, the paste coats the aggregates and bonds them together, gaining strength as it hardens, and concrete is created.
When making concrete, builders use fine aggregate to add volume, while coarse aggregate provides the strength necessary to carry heavy loads. Various chemicals, called admixtures, can also be added to concrete to make different sorts of mixtures.
How is concrete made?
Before concrete is made, the three raw materials must be proportioned correctly to ensure the outcome of a mixture that is strong and sturdy. The components of concrete react differently with each other based on the ratio of how much of each is added, and proportions will differ based on the type of concrete being made. The most common ratio, however, is:
- 10–15% cement
- 60–75% aggregate
- 15–20% water
The concrete mixing process begins with preparing the Portland cement mix. Portland cement is made of a calcareous material (often limestone) that is ground up into a powder, which is then heated and burned in a rotary, turning it into a pebble-like material called “clinker” The clinker is then ground up again until it is a crushed powder, to which gypsum is added.
After the Portland cement is prepared, it is mixed with the aggregates, water, and optional admixtures (the different chemicals or materials that change the consistency and strength of concrete). The ingredients are stirred together well, as to properly coat the aggregates with the cement paste. After combining the materials, the cement is activated by the water, coating the aggregate particles and gaining strength as it hardens in a process called hydration.
16 Common types of concrete
One of the reasons concrete is used to build so many different structures is due to how versatile it is and how it can be molded to any desired shape or design. There are many different types of concrete, however, and they are used for all different sorts of structures. Here are 16 types of concrete and how they are used.
1. Normal strength concrete
Normal strength concrete, or “regular” concrete, is the most common type of concrete with a basic mix of cement, aggregates, and water. Normal concrete has a mixing proportion of 1:2:4 (one part cement, two parts aggregate, four parts water), however, the amount of water used will depend on the humidity of the location and the desired consistency of the concrete. Normal strength concrete is typically used for pavements, home construction projects, and buildings that don’t require maximum tensile strength.
2. Plain concrete
Plain concrete is concrete in its simplest form. It is made using the same mixing proportions as normal strength concrete, but will have absolutely no reinforcement in it. It can be used to build structures that do not require intense tensile strength. Pavements and walkways are common uses of plain concrete.
3. Lightweight concrete
This type of concrete has a lower density and a higher water content than normal concrete. Lightweight concrete is made using lightweight aggregates, such as pumice, clay, or perlite. Since the specific aggregates chosen are what determines the density of the concrete, lightweight concrete is low in density, and is defined as any type of concrete with a density level of less than 1920kg/m3. Lightweight concrete is used in areas where the total “dead weight” of a building can be reduced to help prevent collapse, such as walls or flooring.
4. Ready mix concrete
Ready mix concrete is made at a manufacturing plant and delivered to a construction site using a truck with a mixer attached to it. It usually contains admixtures to make it so the cement doesn’t harden before arriving at the site, and is ready to pour.
5. Polymer concrete
Polymer concrete is concrete in which the lime and shale-based Portland cement is replaced with a polymer binder that cures and hardens, such as a polyester, epoxy mixtures, vinyl ester, acrylics, or many various types of polymer resins. The objective of polymer concrete depends on the type of resin used. Epoxy binders, for example, will aid in less shrinkage during curing while acrylic binders offer weather resistance and quicker setting times. Polymer plastic is stickier than cement, and therefore, when combined in a concrete mix, leads to a concrete of higher tensile strength than one composed of Portland cement. When mixing together a polymer binder with water and aggregates, a chemical reaction occurs that begins the curing process quicker than regular concrete. Polymer concrete has a good resistance to corrosion which is why it is used in swimming pools, sewer structures, and other structures that come into close contact with liquids and corrosion-causing chemicals.
6. Glass concrete
Concrete is referred to as glass concrete when recycled glass is added as an aggregate, or used in places of both fine and coarse aggregates, depending on the desired outcome. Glass aggregates are almost always made from recycled glass and can range in size from a fine talc-like powder to gravel-side pieces to six-inch glass rocks. Glass can be crushed using a glass crushing machine, or used in chunks when mixed with the cement, depending on the desired look. Glass concrete typically has a shiny or “glowing” look to it, which makes it an aesthetically pleasing and highly polished looking option for countertops, floors, and tiles.
7. Reinforced concrete
Reinforced concrete, also known as reinforced cement concrete, is made with reinforced bars, usually rebar, to improve the tensile strength of the concrete. The compressive strength of the concrete paired with the tensile strength of the reinforcement material improves the concrete’s overall durability. Contractors might encounter reinforced concrete in large-scale structures that require an immense amount of tensile strength, such as tall buildings, bridges, dams, or any construction situation that involves a structure needing to carry extremely heavy loads.
8. Pervious concrete
Pervious concrete is a more porous type of concrete that lets water pass through it to groundwater underneath. This type of concrete is used to build roads and pavements and is designed to deal with stormwater buildup and can absorb water at a rate of up to five gallons a minute. There are little to no fine aggregates in this type of concrete, creating more voids for water and air to pass through. This allows stormwater to be filtered through the concrete and pass through into the ground. Pervious concrete can help prevent flooding since the water that would normally flow through storm drains is absorbed by the earth.
9. Prestressed concrete
Prestressed concrete is concrete that has compressive stresses applied to it during production and combines the high tensile strength of steel and the high compressive characteristic of concrete These initial compressive stresses are induced by steel tendons located inside of or adjoining to the concrete and are engineered to counteract the stresses that will eventually be placed upon the concrete during service. Since it has been formed under stress, a prestressed concrete structure will be more balanced and less likely to crack when carrying heavy loads. Bridges, roofs, water tanks, and floor beams are often made using prestressed concrete.
10. Precast concrete
Precast concrete is concrete that is poured in a mold and cured, usually offsite, and then transferred to a construction site. This allows for the concrete to be created in a more controlled environment, like a plant or a factory, with more oversight and surveillance, which is good for quality control. Factories can also use the same molds over and over again, saving time and money. Precast concrete allows for a speedier construction, as it shows up to the construction site ready to be installed without any waiting time for it to gain strength. Precast concrete also improves time efficiency in that the walls of a structure can be made off-site as the foundation is created onsite, resulting in the building being ready for use faster.
11. Air entrained concrete
Air entrained concrete is concrete containing microscopic air bubbles that help to relieve internal pressure in the concrete. An air entraining agent is added during the mixing process, reducing the surface tension and causing air pockets to form in the slurry. This type of concrete is suitable for structures in environments with freeze-thaw conditions, where the temperature shifts from below to above freezing, causing a water buildup. The tiny pockets allow space for water to expand, which prevents cracking and resists scaling in concrete, resulting in a structure that lasts longer over time. The microscopic air bubbles range from 5–7% of the concrete mix, and since adding air to concrete lessens its density, it is common for a higher amount of cement to be used to make up for the strength.
12. High-strength concrete
High strength concrete is any concrete that has a compressive strength of 6000 pounds per square inch (PSI) or higher. It is made using strong, durable aggregates and has a high cement content and lower water to cement ratio, with superplasticizers added to improve any workability issues stemming from stickier concrete. Compared to normal strength concrete, the primary use of high-strength concrete is to reduce the weight, bleeding, and permeability issues, making the structure more resistant to corrosion and chemicals. High-strength concrete is commonly used in the construction of high-rise buildings servicing highly compressive loads.
13. Vacuum concrete
Vacuum concrete is a concrete involving the removal of excess water not needed for the hydration process after the concrete is placed and before the hardening process begins. Mats are placed on filtering pads over the cement, and a vacuum pump is used to extract the excess water. This technique, called vacuum dewatering, lowers the water to cement ratio of the concrete, which gives vacuum concrete a higher strength and durability level compared to normal concrete. It also has a high workability level, despite high strength and workability not usually being achievable simultaneously in concrete. This is due to the excess water, making it easier to pour. After pouring, the water is no longer necessary and is vacuumed out to achieve high strength. Bridge deck slabs and industrial floors are common uses of vacuum concrete.
14. Asphalt concrete
Asphalt concrete is a type of concrete commonly used to make roads, parking lots, and other pavement types. It’s a composite material composed of two primary ingredients: aggregates and liquid asphalt, which are typically combined together at a plant and transported to a paving site and spread by a paving machine followed by being compacted by rollers. The result is a smooth pavement.
15. Rapid set concrete
Rapid set concrete is a type of concrete that hardens at a quicker pace than normal concrete, usually within one to several hours compared to the usual 48 hours. This is because the cement content of rapid set concrete is higher than regular concrete, and also has admixtures added to the mix that work to quicken hydration and the hardening process. Rapid set concrete comes premixed and is ready to use, which is why It is commonly used for non-structural concrete jobs, such as concrete repair and restoration.
16. Self-compacting concrete
Self-compacting concrete, or self-consolidating concrete, is a type of concrete with three key properties: a high filling ability, enabling it to flow with ease throughout the formwork when poured, as dispersed by its own weight; a high passing ability enabling it to pass around any confined spaces and obstructions like steel reinforcement; and segregation resistance, or remaining the same state, during transport, placing, and after placing. These qualities make it so that the concrete sets into the mold very closely without requiring any further assistance or vibration, making it a good option for construction jobs involving less labor and a faster placement time. The fluidity in this type of concrete is due to it being made with a higher count of fine aggregate, usually sand, combined with the use of additives like viscosity-enhancing admixtures and superplasticizers, which ensures that the sand particles are dispersed uniformly. These additives, in addition to the usual ingredients of cement, fine and coarse aggregate, and water, are combined together in a concrete mixer to form this type of concrete.
MT Copeland offers video-based online classes that give you a foundation in construction fundamentals with real-world applications, like how the commercial construction industry works today. Classes include professionally produced videos taught by practicing craftspeople, and supplementary downloads like quizzes, blueprints, and other materials to help you master the skills.