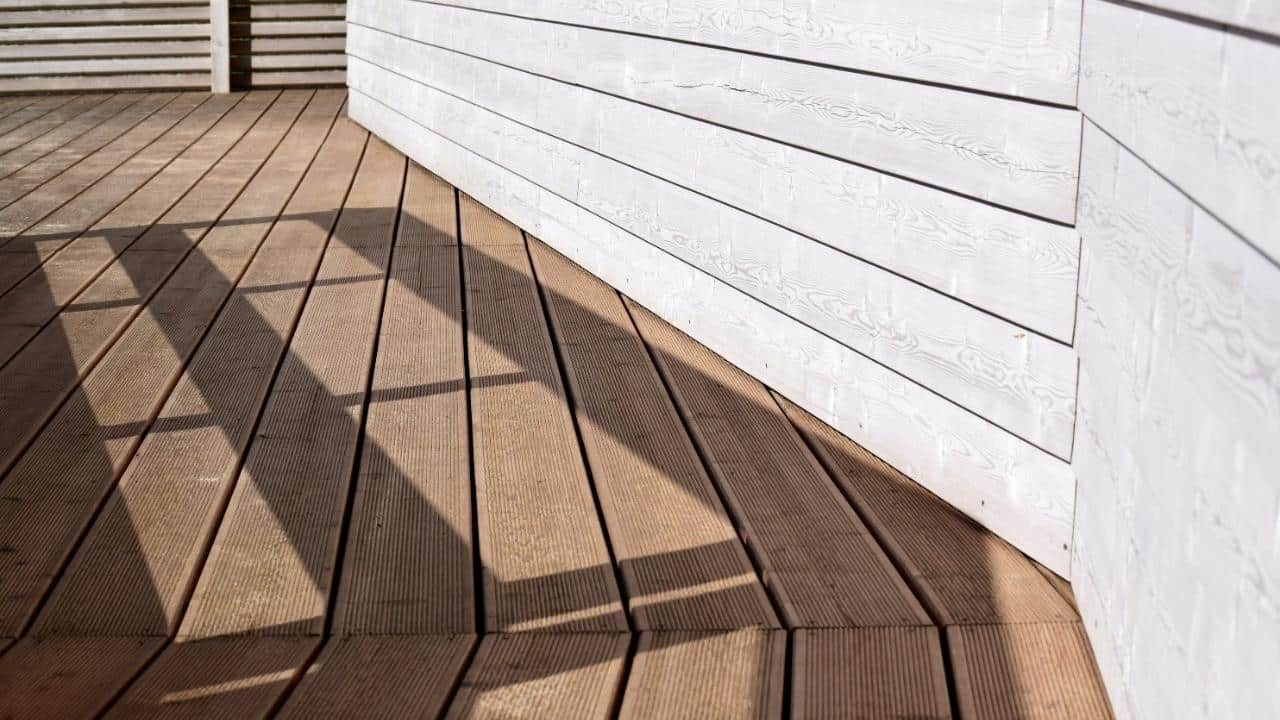
Wood is a plentiful, renewable resource and one that construction crews know well. It can also, however, be difficult to maintain, especially when it is exposed to the elements.
“An option that you have with dimensional lumber is to pressure treat it. This prevents rot and fungus and bugs and other things that can destroy your material over time.” -Professional builder Jordan Smith
Benefits of pressure treated wood
Thanks to its chemical and preservative treatment, pressure treated wood is resistant to many common problems.
- Resistance to rot. The chemical compounds used to pressure treat wood make it resistant to fungi that cause wood to rot.
- Protection from insects. Similarly, treatments repel common insect threats like termites and carpenter ants.
- Cost. Pressure treated wood is more expensive than untreated wood but given that it can last for decades, it often ends up being more economical in the long run.
- Ease of Use. Pressure treated wood, like other woods, is light and can be easily cut and fastened to other supports. Note, however, that it is essential that construction crews use protective equipment including wearing gloves and masks when working with pressure treated wood.
While some tropical hardwoods provide similar resistance, they are typically much more expensive than pressure treated lumber. It is also possible to paint or stain some, though not all, pressure treated woods, providing additional protection.
Where to use pressure treated wood
You may already be familiar with pressure treated wood as decking boards. It’s one example of where you would use it: outside and exposed to the elements. If wood is going to be used indoors, opt for non-treated lumber. The chemicals that make pressure treated wood both water- and insect-resistant can be toxic. Leave it outside!
Southern yellow pine and Douglas fir are commonly used for decks while a handful of other varieties are used for structural work.
For indoor projects where wood is likely to be exposed to humidity or moisture (in bathrooms, for example), select untreated varieties that are more resistant to rot. If they are properly sealed and painted, they should resist cracking, warping, and other water damage.
Learn all about the properties of wood and how wood is used in construction in the MT Copeland course on Wood Materials. Taught by professional builder Jordan Smith, the course covers topics that range from wood hardness and shear strength to joists and laminated veneer lumber.
How is pressure treated wood produced?
The goal of the pressure treatment process is to replace the air in the wood with chemicals that provide resistance to fungal decay, rot, and insects. The pieces of wood are first placed in a depressurized chamber to extract any air. Chemicals are then sprayed on, under pressure to assure that they reach the core of every piece. After the wood is saturated, it is allowed to dry which may take anywhere from two days to two weeks. “When it shows up on your job site,” Smith explains. “It’s wet, it’s really wet.”
What Chemicals Are Used In Pressure Treating?
Alkaline copper quat (ACQ). ACQ is a recently developed family of compounds of copper and quaternary ammonium: You may come across references to ACQ-B, -C, and -D. Each has its particular strengths.
Ammoniacal copper zinc arsenate (ACZA). ACZA includes copper, zinc, and arsenic. Because it is effective at treating Douglas fir, it’s an especially common option in the western United States.
Wood is a plentiful, renewable resource and one that construction crews know well. It can also, however, be difficult to maintain, especially when it is exposed to the elements.
“An option that you have with dimensional lumber is to pressure treat it. This prevents rot and fungus and bugs and other things that can destroy your material over time.” -Professional builder Jordan Smith
Benefits of pressure treated wood
Thanks to its chemical and preservative treatment, pressure treated wood is resistant to many common problems.
- Resistance to rot. The chemical compounds used to pressure treat wood make it resistant to fungi that cause wood to rot.
- Protection from insects. Similarly, treatments repel common insect threats like termites and carpenter ants.
- Cost. Pressure treated wood is more expensive than untreated wood but given that it can last for decades, it often ends up being more economical in the long run.
- Ease of Use. Pressure treated wood, like other woods, is light and can be easily cut and fastened to other supports. Note, however, that it is essential that construction crews use protective equipment including wearing gloves and masks when working with pressure treated wood.
While some tropical hardwoods provide similar resistance, they are typically much more expensive than pressure treated lumber. It is also possible to paint or stain some, though not all, pressure treated woods, providing additional protection.
Where to use pressure treated wood
You may already be familiar with pressure treated wood as decking boards. It’s one example of where you would use it: outside and exposed to the elements. If wood is going to be used indoors, opt for non-treated lumber. The chemicals that make pressure treated wood both water- and insect-resistant can be toxic. Leave it outside!
Southern yellow pine and Douglas fir are commonly used for decks while a handful of other varieties are used for structural work.
For indoor projects where wood is likely to be exposed to humidity or moisture (in bathrooms, for example), select untreated varieties that are more resistant to rot. If they are properly sealed and painted, they should resist cracking, warping, and other water damage.
Learn all about the properties of wood and how wood is used in construction in the MT Copeland course on Wood Materials. Taught by professional builder Jordan Smith, the course covers topics that range from wood hardness and shear strength to joists and laminated veneer lumber.
How is pressure treated wood produced?
The goal of the pressure treatment process is to replace the air in the wood with chemicals that provide resistance to fungal decay, rot, and insects. The pieces of wood are first placed in a depressurized chamber to extract any air. Chemicals are then sprayed on, under pressure to assure that they reach the core of every piece. After the wood is saturated, it is allowed to dry which may take anywhere from two days to two weeks. “When it shows up on your job site,” Smith explains. “It’s wet, it’s really wet.”
What Chemicals Are Used In Pressure Treating?
Alkaline copper quat (ACQ). ACQ is a recently developed family of compounds of copper and quaternary ammonium: You may come across references to ACQ-B, -C, and -D. Each has its particular strengths.
Ammoniacal copper zinc arsenate (ACZA). ACZA includes copper, zinc, and arsenic. Because it is effective at treating Douglas fir, it’s an especially common option in the western United States.
Borate preservatives. Borates are salts including sodium octaborate, sodium tetraborate, and sodium pentaborate. Given borates’ water solubility, these woods should not be used for ground contact uses as the borate will leach out.
Copper azole (CBA). Copper azole formulas include amine copper and co-biocides. In some cases ammonia is added for woods that are difficult to penetrate, like Douglas fir.
Chromated Copper Arsenic (CCA). Given concerns over its toxicity, this once popular treatment is no longer used in residential projects. (It is still used in some commercial and industrial structures.)
Oil-Type Treatments. Creosote, pentachlorophenol, and copper naphthenate are oil-type wood preservatives. Because these treatments result in wood that is oily to the touch and often has an unpleasant odor, it is typically used for utility poles, pilings, and in other places where human contact will be infrequent.
3 Types of pressure treated wood
- Above ground: Some types of pressure treated wood (like those using borates) will leach out the preservative used to treat them if exposed to moisture or standing water. These above-ground woods are often used when insect resistance, and not rot, is the primary concern.
- Ground contact: A piece of lumber that has been treated so that it effectively retains the chemicals used to preserve it is safe for “ground contact.” Ground contact pressure treated wood can last for up to 40 years, even under wet conditions.
- Marine lumber: This extremely resistant type of pressure treated wood is generally reserved for docks, seawalls, and other seaside locations.
Grades of pressure treated wood
Pressure treated wood is sold with the lumber grades Premium, Select, Number 1, Number 2, and Number 3. The higher the grade, the fewer the defects—that is splits or knots. In general, you will want to choose Number 2 grade boards, or higher, for decks.
AWPA Use Categories: The American Wood Preservers’ Association has a 12-tier system for identifying wood uses ranging from UC1 and UC2, intended for interior use, up to UC5 (wood that can be immersed in saltwater). Many of these categories are further subdivided: For example, UC5A is intended for colder northern waters while UC5C covers wood that is suited to the Gulf Coast.
Retention Levels: Pressure treated wood’s retention level indicates its ability to retain, as opposed to leaching, the chemicals that it has been treated with. This scale ranges from 0.25 for above ground wood to 2.5 for wood immersed in saltwater.
MT Copeland offers video-based online classes that give you a foundation in construction fundamentals with real-world applications. Classes include professionally produced videos taught by practicing craftspeople, and supplementary downloads like quizzes, blueprints, and other materials to help you master the skills.