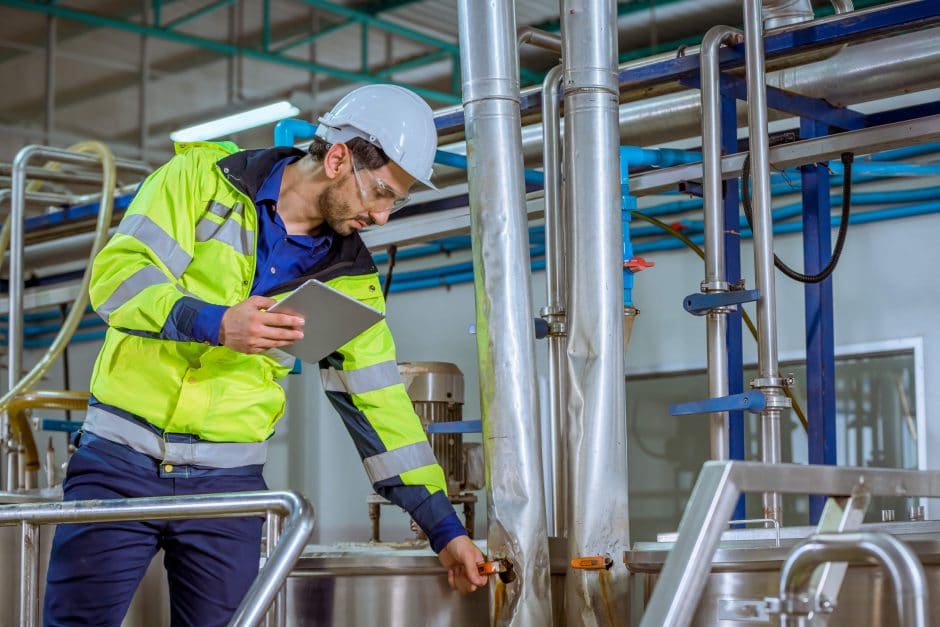
Quantity takeoff is an in-depth estimate of all the inputs required for a construction project. This provides the foundation for determining costs by itemizing how much material and labor will be needed. Like many elements of the construction industry, technology has paved the way for faster and more accurate calculations.
What is quantity takeoff?
A quantity takeoff is an early part of the bidding process that defines the amount of work that will be required for a given project. A quantity takeoff includes the material requirements for a project, as well as the f labor and equipment needed to complete the work. It does not, however, include the construction costs, it only quantifies the work and resources needed to complete a project, not how much it will cost. A takeoff simply focuses on the amount of work and resources necessary for the job.
Consider a quantity takeoff for building a concrete foundation. You would need to account for the physical materials, like the reinforcing materials and concrete. You’d also calculate the number of hours or days required of the crew and equipment. The project estimates would only include the quantity of how much is needed—not the costs involved.
A number of people could be involved with a quantity takeoff, including contractors, architects, and engineers. It’s an early step in figuring out the scope and cost of a project. Once a takeoff is complete, a construction cost estimator uses the information to create a budget or proposal for the project.
There are several common terms you may hear during the takeoffs process of a construction project, including:
- Construction takeoff
- Material counts
- Estimating takeoff
- Material estimating
- Quantity surveying
Sometimes these terms are used interchangeably to mean the same thing: a quantity takeoff.
Manual takeoffs vs. digital takeoffs: What’s the difference?
There are two approaches to quantity takeoffs in the construction industry: a manual and a digital process.
- The manual approach requires the estimator to look at physical blueprints and measure all of the materials and surface area for the project. It takes a good deal of experience and precision to accurately estimate the materials and labor with this approach. Additionally, the process is quite time-consuming.
- A digital approach, on the other hand, offers a better chance to gather accurate data for your quantity takeoff. Takeoff software typically has the ability to read blueprints and other design documents. Then it automatically gleans the materials required for the project. These automated construction estimators significantly reduce the risk of error.
One downside is that estimating labor with digital software is limited. Some elements may have labor estimates attached, but only in the most advanced software. Plus, this feature isn’t available for all tasks, making manual calculations necessary for at least some parts of the takeoff.
Whichever approach you choose, be sure to double check the estimates, even with a digital takeoff. It’s hard to completely replace on-the-ground experience and knowledge.
Quantity takeoff is an in-depth estimate of all the inputs required for a construction project. This provides the foundation for determining costs by itemizing how much material and labor will be needed. Like many elements of the construction industry, technology has paved the way for faster and more accurate calculations.
What is quantity takeoff?
A quantity takeoff is an early part of the bidding process that defines the amount of work that will be required for a given project. A quantity takeoff includes the material requirements for a project, as well as the f labor and equipment needed to complete the work. It does not, however, include the construction costs, it only quantifies the work and resources needed to complete a project, not how much it will cost. A takeoff simply focuses on the amount of work and resources necessary for the job.
Consider a quantity takeoff for building a concrete foundation. You would need to account for the physical materials, like the reinforcing materials and concrete. You’d also calculate the number of hours or days required of the crew and equipment. The project estimates would only include the quantity of how much is needed—not the costs involved.
A number of people could be involved with a quantity takeoff, including contractors, architects, and engineers. It’s an early step in figuring out the scope and cost of a project. Once a takeoff is complete, a construction cost estimator uses the information to create a budget or proposal for the project.
There are several common terms you may hear during the takeoffs process of a construction project, including:
- Construction takeoff
- Material counts
- Estimating takeoff
- Material estimating
- Quantity surveying
Sometimes these terms are used interchangeably to mean the same thing: a quantity takeoff.
Manual takeoffs vs. digital takeoffs: What’s the difference?
There are two approaches to quantity takeoffs in the construction industry: a manual and a digital process.
- The manual approach requires the estimator to look at physical blueprints and measure all of the materials and surface area for the project. It takes a good deal of experience and precision to accurately estimate the materials and labor with this approach. Additionally, the process is quite time-consuming.
- A digital approach, on the other hand, offers a better chance to gather accurate data for your quantity takeoff. Takeoff software typically has the ability to read blueprints and other design documents. Then it automatically gleans the materials required for the project. These automated construction estimators significantly reduce the risk of error.
One downside is that estimating labor with digital software is limited. Some elements may have labor estimates attached, but only in the most advanced software. Plus, this feature isn’t available for all tasks, making manual calculations necessary for at least some parts of the takeoff.
Whichever approach you choose, be sure to double check the estimates, even with a digital takeoff. It’s hard to completely replace on-the-ground experience and knowledge.
What to look for in a quantity takeoff
Completing a quantity takeoff requires a good deal of math, and some steps are easier than others. Here’s an overview of the different types of measurements that will likely arise during the process.
- Unit count. A unit count involves estimating all the physical materials required for the project, such as number of doors, handles, sinks, and light fixtures—every item that will be installed in the building. It’s a great first step before estimating costs because later you’ll be able to multiply each unit’s number by its individual price.
- Linear length. The next part of the takeoff is estimating the linear length of materials like pipes and lumber. You wouldn’t calculate how many pieces of PVC pipes are needed; instead, you would extrapolate the length required based on the blueprints.
- Surface area. Materials like flooring and sheetrock require an estimate of the surface area. The equation is the length of the area multiplied by the width. For instance, a room measuring 12 by 18 feet would have a surface area of 216 square feet.
- Weight. Not only do you need to know the amount of materials a project requires, a takeoff includes its gross weight. This is required for a transportation estimate as well.
- Cubic volume. This measures three-dimensional materials like poured concrete or earthworks. The equation is length multiplied by width and by height.
Advantages of quantity takeoffs
Calculating a quantity takeoff for a project comes with three distinct benefits.
- More accurate cost estimates. Perhaps the biggest advantage of kicking off a project with a quantity takeoff is that your cost estimates will be more accurate. You’ll know everything that’s required to complete the project and not have to ballpark your estimate. With all of the relevant quantities on hand, you’ll simply need to research supply prices and multiply that by the number you need in order to calculate costs. Plus, you’ll know if your project qualifies for any bulk-ordering discounts.
- Better communication. Providing your potential client with a detailed quantity takeoff gives them everything they need to make an informed decision. A price quote and no justification may cause friction between you and the client, however, an accurate budget with a line-by-line breakdown of materials, labor, and equipment provides leverage in budget negotiations. It’s a great way to build trust at the beginning of a project and may help you win bids.
- Saved time. An accurate quantity takeoff saves time that is usually stolen by a lack of materials or the wrong materials being delivered to the jobsite. Plus, with slow shipping times and product shortages worldwide, an in-depth takeoff can help you figure out the lead time for everything you need.
Final thoughts
A quantity takeoff takes a good bit of skill and effort. But the extra work will pay off when you’re able to provide clients with accurate information that helps them make smarter decisions. It provides added value and helps everyone stay on track with deadlines and budget.
MT Copeland offers video-based online classes that give you a foundation in construction fundamentals with real-world applications, like how to prepare a construction estimate. Classes include professionally produced videos taught by practicing craftspeople, and supplementary downloads like quizzes, blueprints, and other materials to help you master the skills.