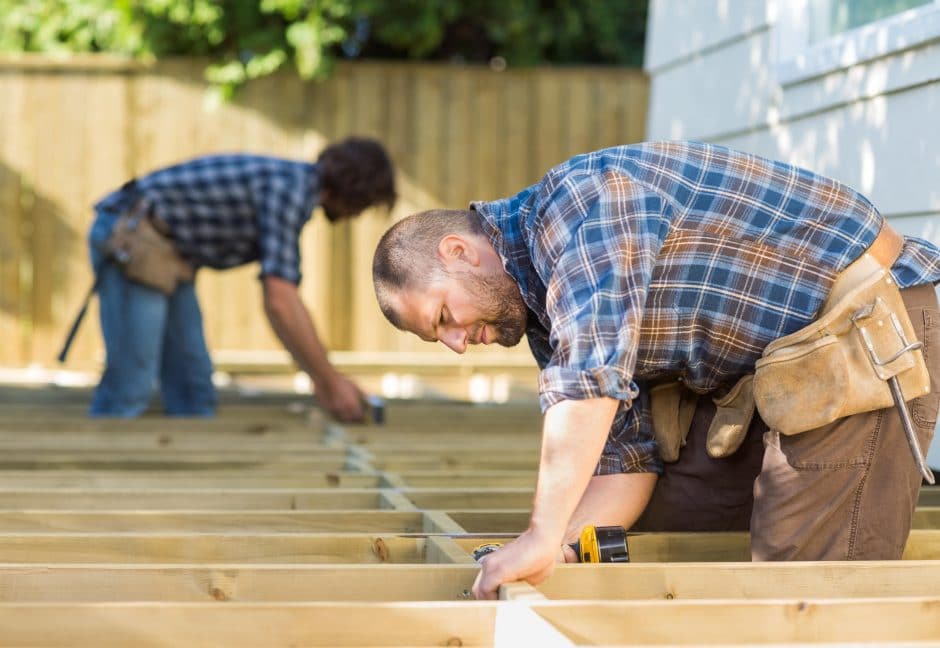
Estimating the cost to build a deck is a multifaceted endeavor: You’ll need to consider the number of square feet, height above ground, site conditions, materials, and labor costs. In the US, the average cost per square foot to build a deck is about $30 to $60. So for a standard 200 square foot deck, you can expect to pay around $6,000. Custom designs, seismic requirements, and high demand in your area can push those costs even further.
“However, deck costs are a really hard thing to wrap your head around,” says professional deck builder and MT Copeland instructor Mike Guertin. “It’s not something that can be generalized at all.”
To start sketching out a budget, research the cost of your preferred materials and labor rates in your area. You can also ask friends and family who’ve had a deck built. If they are comfortable sharing the cost breakdown or contractor’s quote, you’ll get a more accurate idea of cost versus an online calculator, which relies on national average costs.
Labor
Labor is the single-greatest factor in the cost of building a deck—about half the total cost to build, Mike says. Hourly wages differ by city and state, but generally, if you live in a big city with a greater demand, you’ll face higher rates. Here are a few other factors that can impact your labor cost:
- Site condition: It takes more resources for a team of builders to safely navigate a treacherous build site and travel long distances for daily work. If your home is remote and/or hard to access, or the build site is on a steep grade, labor costs may be greater.
- Height above grade: It takes additional time to build a deck when you have to set up a lot of staging or scaffolding to reach the work level. If you’re working at human height (five feet or lower) and can use short ladders, the labor cost isn’t much greater than building a grade-level deck. Once you get above five feet, it will take more time to stage and build, and the cost will increase as the elevation of the deck increases, Mike says. Depending on the version of the model building code your local jurisdiction follows, some structural elements of the deck, like post size and lateral bracing, may increase, adding additional labor and material costs. Some code jurisdictions also require a registered engineer to design structural elements of elevated decks, further adding to the total cost.
- DIY vs. hiring a contractor: If you have the time and skillset to build a code-compliant deck, you can save on some or all of the labor cost of a project. As Mike notes, “I have seen many DIY-built decks that far exceed the quality of a deck built by professionals who don’t know what they’re doing.”
Materials
Like any home improvement project, materials costs vary greatly. Mike notes that due to the pandemic, lumber prices rose 4x from December 2019 to May 2021. As of September 2021, some composite decking materials were on backorder six to 12 weeks. “Material prices fluctuate due to supply and demand,” says Mike, “so you may be able to save on material costs by delaying a deck building project until prices moderate.”
Be sure to check the availability of your preferred decking and railing materials when planning a project so you can time the construction schedule to coincide with material delivery.
Framing materials
Framing materials are the structure or backbone of a deck and include posts, joists, and hardware—i.e., the entire substructure or the deck’s structure beneath what’s visible to the owner. Pressure-treated dimensional lumber (ideally ground contact lumber) is the most conventional choice for framing and the least expensive. Engineered wood, steel, and aluminum framing materials are often more costly but have other performance characteristics like being straighter, flatter, stiffer and less prone to seasonal movement than treated dimensional lumber.
If you build an elevated deck with visible framing, you may want to choose a more aesthetically pleasing wood like redwood or cedar. Just remember, using premium wood materials for your deck adds a cost that’s 20% to 30% higher than pressure-treated lumber.
Beyond aesthetics, the cost of footing materials is strongly tied to local climate. If you’re in a cold climate, footings need to be buried below the frost line so that they do not move or heave when the ground freezes and thaws throughout the seasons. Digging deeper and using more materials will likewise raise costs—though they aren’t required for warm climates that have shallow (or no) frost lines. “It’s easy to spend many thousands of dollars in cold climates on footings that a warm-climate deck would not require,” Mike explains.
Decking materials
Decking refers to the boards or panels that make up the floor of your deck, so wood or composite materials similarly impact deck construction costs.
Estimating the cost to build a deck is a multifaceted endeavor: You’ll need to consider the number of square feet, height above ground, site conditions, materials, and labor costs. In the US, the average cost per square foot to build a deck is about $30 to $60. So for a standard 200 square foot deck, you can expect to pay around $6,000. Custom designs, seismic requirements, and high demand in your area can push those costs even further.
“However, deck costs are a really hard thing to wrap your head around,” says professional deck builder and MT Copeland instructor Mike Guertin. “It’s not something that can be generalized at all.”
To start sketching out a budget, research the cost of your preferred materials and labor rates in your area. You can also ask friends and family who’ve had a deck built. If they are comfortable sharing the cost breakdown or contractor’s quote, you’ll get a more accurate idea of cost versus an online calculator, which relies on national average costs.
Labor
Labor is the single-greatest factor in the cost of building a deck—about half the total cost to build, Mike says. Hourly wages differ by city and state, but generally, if you live in a big city with a greater demand, you’ll face higher rates. Here are a few other factors that can impact your labor cost:
- Site condition: It takes more resources for a team of builders to safely navigate a treacherous build site and travel long distances for daily work. If your home is remote and/or hard to access, or the build site is on a steep grade, labor costs may be greater.
- Height above grade: It takes additional time to build a deck when you have to set up a lot of staging or scaffolding to reach the work level. If you’re working at human height (five feet or lower) and can use short ladders, the labor cost isn’t much greater than building a grade-level deck. Once you get above five feet, it will take more time to stage and build, and the cost will increase as the elevation of the deck increases, Mike says. Depending on the version of the model building code your local jurisdiction follows, some structural elements of the deck, like post size and lateral bracing, may increase, adding additional labor and material costs. Some code jurisdictions also require a registered engineer to design structural elements of elevated decks, further adding to the total cost.
- DIY vs. hiring a contractor: If you have the time and skillset to build a code-compliant deck, you can save on some or all of the labor cost of a project. As Mike notes, “I have seen many DIY-built decks that far exceed the quality of a deck built by professionals who don’t know what they’re doing.”
Materials
Like any home improvement project, materials costs vary greatly. Mike notes that due to the pandemic, lumber prices rose 4x from December 2019 to May 2021. As of September 2021, some composite decking materials were on backorder six to 12 weeks. “Material prices fluctuate due to supply and demand,” says Mike, “so you may be able to save on material costs by delaying a deck building project until prices moderate.”
Be sure to check the availability of your preferred decking and railing materials when planning a project so you can time the construction schedule to coincide with material delivery.
Framing materials
Framing materials are the structure or backbone of a deck and include posts, joists, and hardware—i.e., the entire substructure or the deck’s structure beneath what’s visible to the owner. Pressure-treated dimensional lumber (ideally ground contact lumber) is the most conventional choice for framing and the least expensive. Engineered wood, steel, and aluminum framing materials are often more costly but have other performance characteristics like being straighter, flatter, stiffer and less prone to seasonal movement than treated dimensional lumber.
If you build an elevated deck with visible framing, you may want to choose a more aesthetically pleasing wood like redwood or cedar. Just remember, using premium wood materials for your deck adds a cost that’s 20% to 30% higher than pressure-treated lumber.
Beyond aesthetics, the cost of footing materials is strongly tied to local climate. If you’re in a cold climate, footings need to be buried below the frost line so that they do not move or heave when the ground freezes and thaws throughout the seasons. Digging deeper and using more materials will likewise raise costs—though they aren’t required for warm climates that have shallow (or no) frost lines. “It’s easy to spend many thousands of dollars in cold climates on footings that a warm-climate deck would not require,” Mike explains.
Decking materials
Decking refers to the boards or panels that make up the floor of your deck, so wood or composite materials similarly impact deck construction costs.
As with framing, pressure-treated wood decking is the most common and least expensive choice. Premium woods such as redwood, Ipe, cedar, and Tigerwood are stunning and durable, but more expensive. Synthetic decking like cellular PVC and wood/plastic composite is a popular choice. This type of decking lasts longer and requires less maintenance than pressure-treated wood decking but costs more.
Design features
Design costs are entirely driven by the homeowner. As you might expect, a simple design will be more cost effective, but those with a more ambitious vision may splurge on a professional deck designer to deliver a dream deck.
A basic single-level rectangular deck surface is the cheapest option. Any design element that requires changes to the framing—like a hot tub that needs its weight supported—will raise the cost. Special design elements such as built-in seating, curved designs, multiple deck levels, pergolas and custom lighting or skirting will cost extra, as will accommodating add-ons like outdoor kitchens, fireplaces or fire pits, or sound systems.
Other costs
Although labor and materials are the biggest factors in determining deck cost, keep these potential other costs in mind, especially if you plan to DIY:
- Railing: The deck building code section of the International Residential Code requires a guard railing system for decks that are greater than 30 inches above the surrounding earth surface. Beyond code requirements, there are endless design options for deck railings.
- Permits: Local jurisdictions determine building permit requirements. Your jurisdiction may not require a building permit, so your cost will be zero. In other areas, the size and the scope of the deck or the cost of construction determines the permit price.
- Taxes and insurance: Adding a deck may increase your property taxes or your homeowner’s insurance premium. However, decks typically increase the value of a home.
- Deck removal: If you’re replacing an existing deck, expect extra labor costs for demo and disposal.
- Seismic zones: If you live in a seismic zone, your local building department might require a structural engineer to certify the deck design.
- Stairs: If your deck requires stairs for access, this will raise material and labor costs.
MT Copeland offers video-based online classes that give you a foundation in construction fundamentals with real-world applications, like how to build a freestanding deck. Classes include professionally produced videos taught by practicing craftspeople, and supplementary downloads like quizzes, blueprints, and other materials to help you master the skills.